前回に引き続き基板作成を行います。
今回も、基板を量産するわけではないので、自作CNCで基板を作成します。
スペース的には厳しいので両面基板で仕上げます。
■ レベリング
前回は紹介できませんでしたが、基板を切る前に均一な深さでパターンを切るために、レベリングします。動画を見ていただければわかると思いますが、レベリング自体の仕組みは簡単で基板をいくつかのメッシュに分解して、計測位置からの距離に応じて高さを補完して求めます。
DIYレベルのCNCで、両面基板を作成するためには、スキュー補正、レベリングは必須の機能になると思います(素人考えです)。
相当な組付け精度で作られた機械であれば不要かもしれませんが、カミソリも入っていないようなCNCなので、実用レベルとするには、このようなソフト的な補強が必要になると思います。
■ 基板の切り出し
基板切り出し風景を添付します。
表裏と同じことを行うのですが、動画は表面の作成風景です。(裏面は長いので省略しました)
ちなみに、両面基板を作成する場合には、穴は貫通させず、表面、裏面からドリングを半分づつ行います。なんでこんな面倒なことをやるかというと、理由は以下の2点です。
a. 穴貫通時の裏面破壊防止
片側からのみ穴をあけた場合、下記のように反対側がドリルに押されて飛び出してきます。
片面基板であれば問題ないのですが、両面基板の場合は、反対側にパターンがあるので、致命的です。
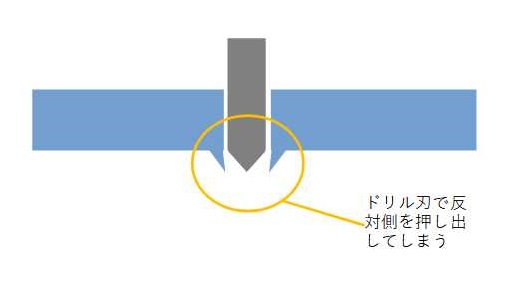
b. 穴ずれによるパターン破壊防止
片面からのみ穴をあけると、下図のように位置が、少し(0.1mm程度)でもずれていると下図のように反対面のパターンを壊してしまうことがあります。スキュー補正していても、極わずかですが、刃物のブレや計測誤差などあるので、貫通穴は危険です。
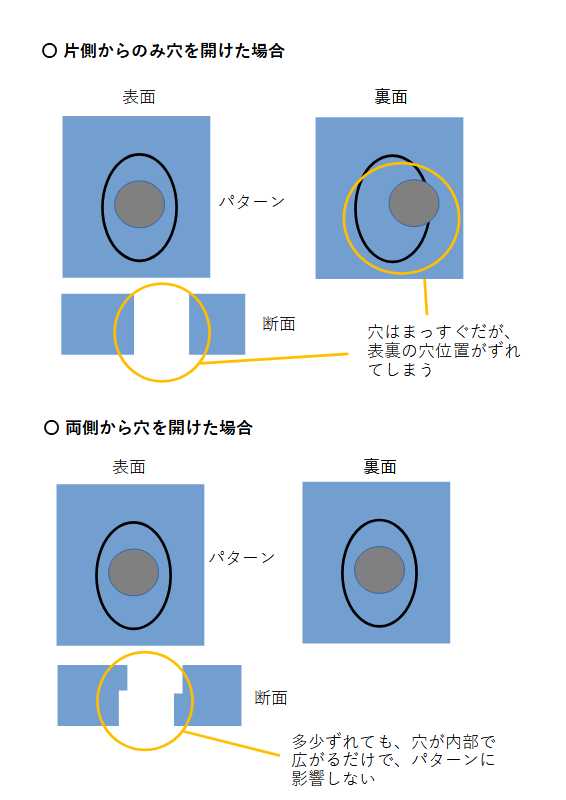
■ 基板カット結果
今まで説明してきたような工程を経て作成した基板は下記です。
少し、スペースがキツキツなので、隣のパターンに押されている箇所はありますが、問題なしです。
最小幅0.2mm程度で基板がカットできました。ちなみに、今回使った刃は、これで、普通精度の刃になりました。2度と0.2mmのパターンを切ることはできません。(研いだら、いけるのかなぁ~?)
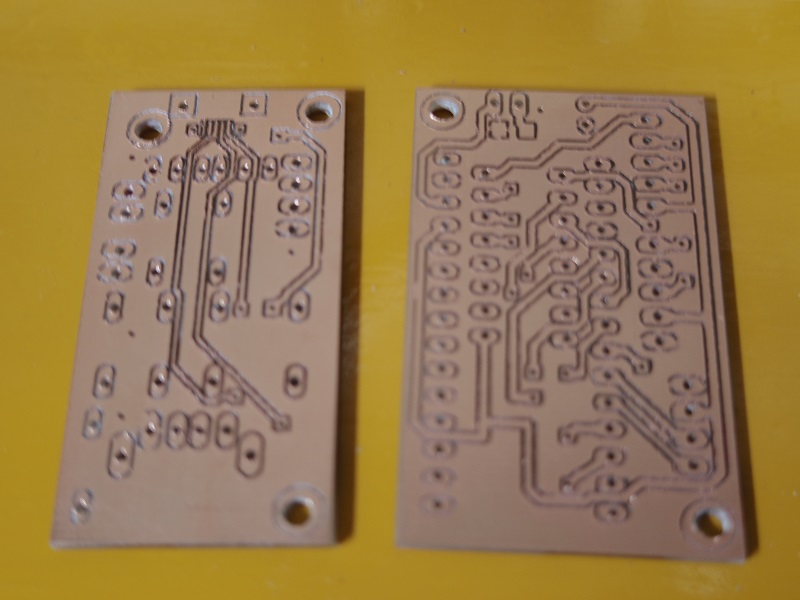
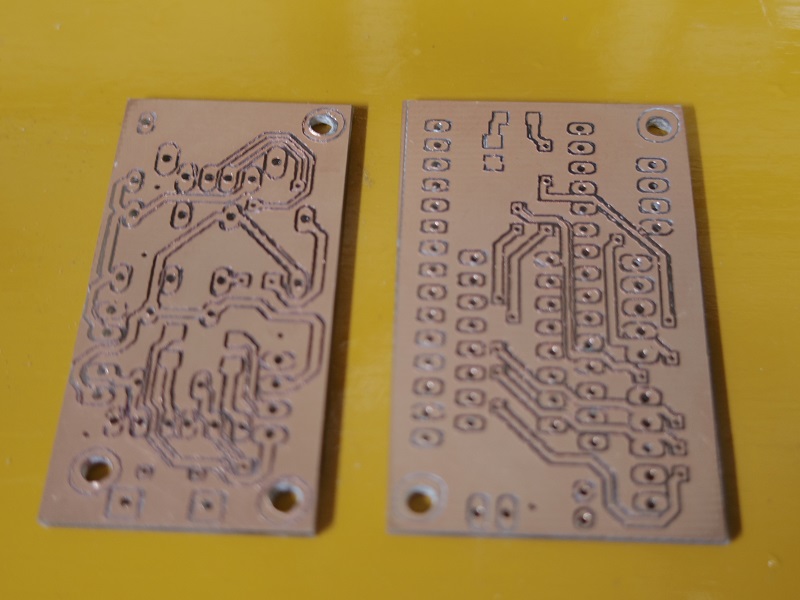
■ レジデントマスク
あとは、地味にレジデントマスクをかけて基板を仕上げていきます。
数年前までは、黒とか白のレジデントマスクが手に入り、粗が見えず、きれいに仕上がったのですが、最近は緑しか手にはいらないのと、手に入ってもマスクが弱くて、使いにくいです。
今後はどんなレジデントマスクでも、きれいに仕上がるように、工夫する必要がありますねぇ・・・
まだ、この辺りのプロセスは、発展途上です。
塗り終わりは、かきのような感じになりました。
ドリル穴の掃除が今一でレジデントマスクが詰まっていました。後で掃除しておきました。(笑)
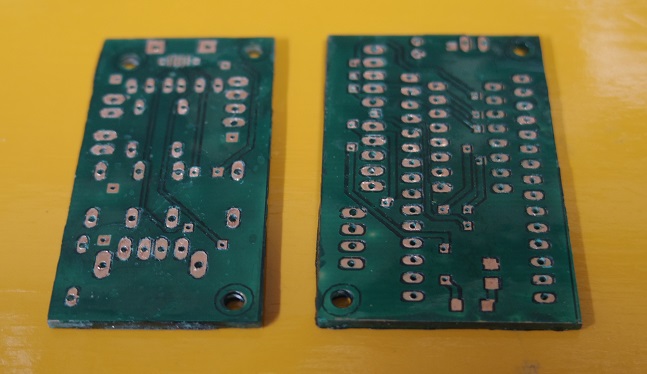
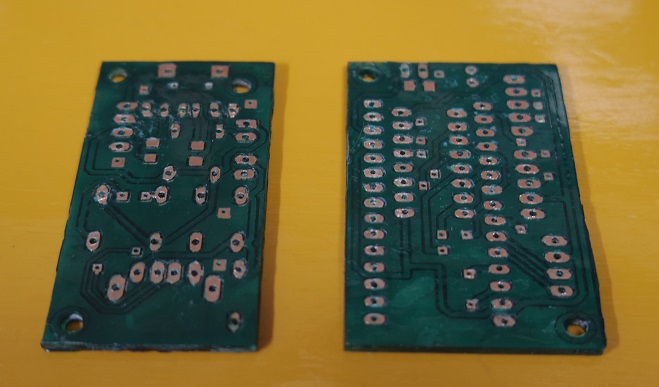
■ 次回
次回は、基板に部品実装し、実際に動作テストを行っていこうと思います。
しばらく、個人的な理由で時間が取れず、不定期更新になるかもしれないですが、でき次第掲載する予定です。もしよかったら、またのぞいてやってください。