制作過程を紹介します。
制作過程と、組み立て風景なので面白くないかもしれませんが、何かの参考になれば幸いです。
■ 3D モデリング
まずは、アイデアを絵にしていくところからスタートです。
一番試行錯誤が多く、時間のかかる工程です。
3D CADを正規に習ったことはないので、自己流です。
私のやり方は、最初に装着対象物の(必要な部分の)3Dモデルを起こします。
複雑すぎて、かなり面倒な場合もありますが、できるだけ採寸可能な3Dモデルを起こします。
(3Dスキャナとかあると便利そうだと思いますが、実用性のあるものは高いので手が出ません。)
色々な方法がありますが、今回は対物レンズ付近のサイズがわかればよいので、ノギスで対物レンズ径を計測し、3Dモデルを起こしました。
ここまでできれば、あとは、自分のアイデアに沿ってひたすら3Dモデル上に様々な部品をのっけていきます。過去の経験(部品強度、部品間のあそび等)をもとに、部品の3Dモデルをつくっていきます。
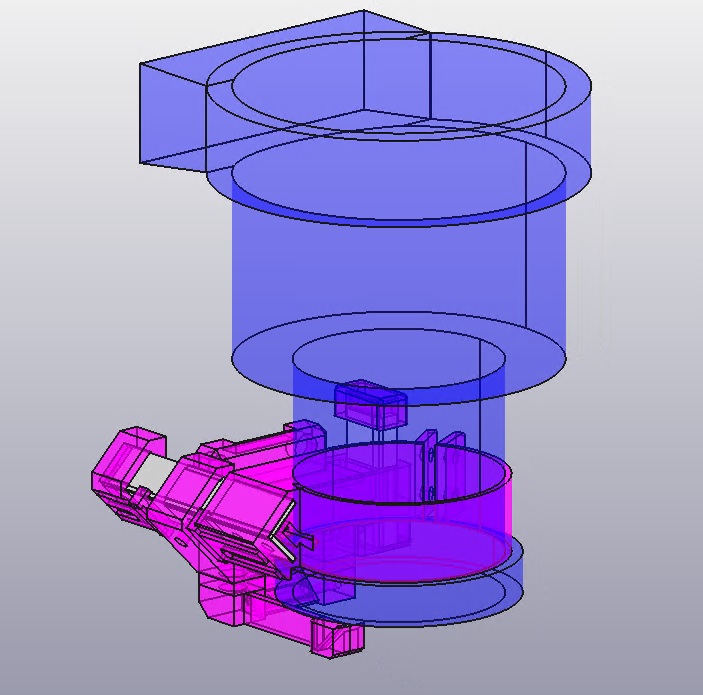
同様に基板なども、ケースサイズ、PCB上の部品サイズから大きさを決めていきます。
私の場合は、基板にあわせてケースをつくるというよりは、ケースに合わせて基板を作る方がおおいです。
今回はESP32が意外に大きくて、おさまりが悪かったので、コントローラ基板(ESP32基板)、パネル基板、ロータリーエンコーダ基板の3つに分割して納めました。
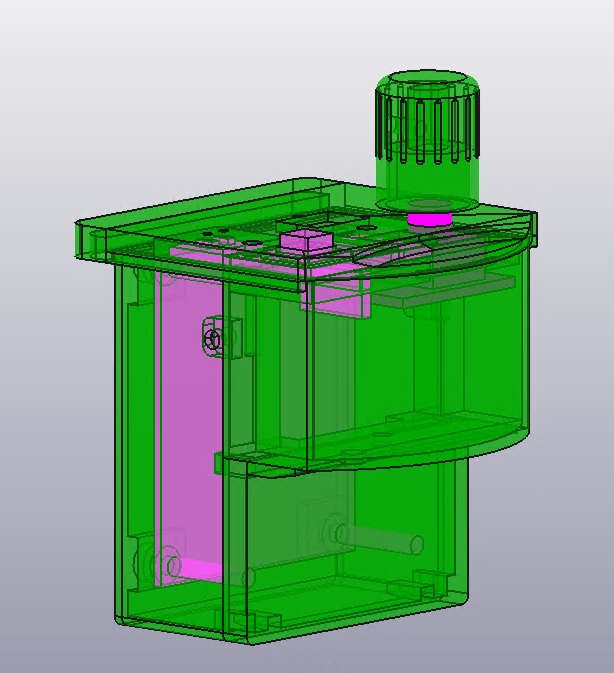
私の場合、3Dプリンタ部品、CNC部品、木工、部屋のレイアウト等は、3D CADで設計することが多いです。
私が、普段使用しているのは、FreeCADで、3Dプリンタを使い始めたころから、ずっとこれを使っていて、困らないので使い続けてます。
たまに不具合もありますが、商用利用もフリーソフトなのと、便利なアドイン等もあるので、幅広く使うことができ、便利だと感じてます。
■ 基板設計
3Dモデルが出来上がったところで回路設計、基板デザインを行います。
回路設計が終わったところで、ブレッドボード上で、ファームウェアとともに動作テストします。
基本的なバグをつぶした後に、基板デザインに移行します。例として、下記にパネル基板を示します。
パネル基板は、ケース形状の制約で基板レイアウトの緑の線で囲われた形状(約27.5mm四方)の両面基板でデザインしてあります。
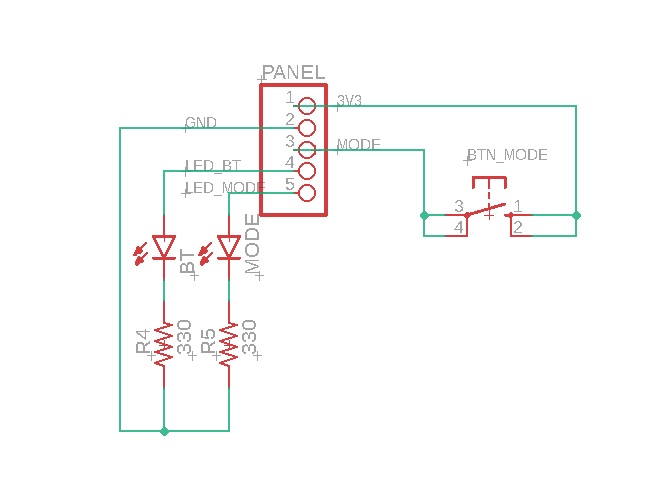
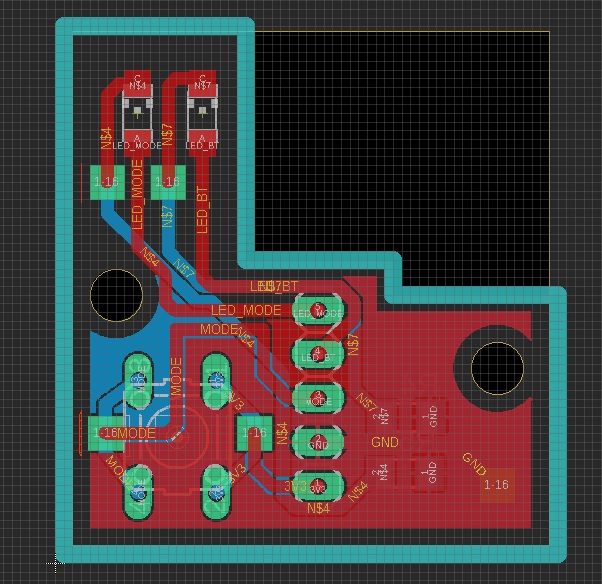
私の場合、基板設計は、AUTODESK EAGLEを使用しています。
理由は、商用利用でなければフリーであることと、CNC用の基板制作コード(grbl)が生成できるからです。
私の場合、今回のように1品モノ、両面基板、0.5mm配線程度であれば、自作基板制作用CNCで製造します。場合によっては、ユニバーサル基板を使うこともあります。
大量に基板が必要な場合や0.5mm未満の配線が必要な場合は、海外の格安PCB製造会社にお願います。
海外のPCB製造会社にお願いすれば、きれいにできますし、値段もリーズナブルですが、製造から到着まで2週間くらいかかるので、きれいに仕上げたいとか、大量生産が必要とかでなければ、DIYで済ませます。
今回も、ESP32の型番をミスって、コントローラ基板を1度作り直していますが、次の日には修正基板は出来上がっていたので、時間的ロスを最短に抑えることができたと考えています。
手前みそですが、自作基板制作用CNCとはいっても、レベリング、スキュー補正、ドリリング、手動ツールチェンジ、ミリングを行え、かつ、片面、両面基板対応の優れモノなので気に入ってます。
自作品なのでハードもソフトも仕組みがわかっていることもあり、好きに機能インプリも可能です。
今回は撮影していないですが、機会がありましたら制作過程など紹介しようと思います。
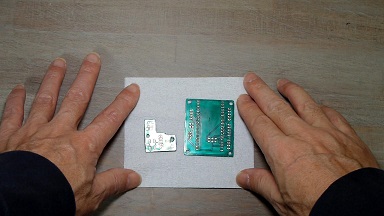
■ コントローラ組み立て
まずは、構成部品の紹介。
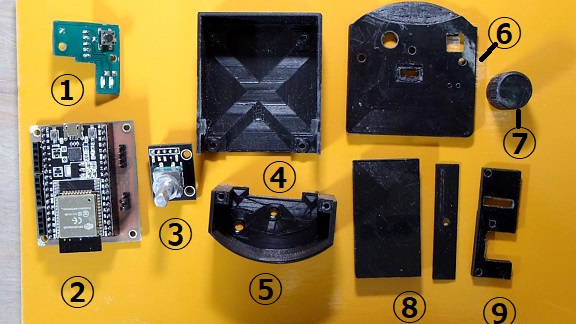
① パネル基板
インジケータ、ボタンを搭載した基板です。ESP32コントローラ基板のユーザーIFです。
② ESP32コントローラ基板
ESP32を使用したコントローラ基板です。
③ ローターリーエンコーダーモジュール
ロータリーエンコーダーモジュールです。今回は部品搭載されたモジュールを使用ました。
④ コントローラケース
ESP32コントローラを収めるケースです
⑤ パネルケース
パネル基板、ロータリーエンコーダーを収めるケースです。
⑥ パネルカバー
パネル基板、ローターリーエンコーダーのカバーです。
⑦ ロータリーエンコーダーノブ
ロータリーリーエンコーダーのノブです。
⑧ コントローラカバー
コントローラーケースのカバーです。2つの部品を組み立てて使います。
⑨ パネル内部仕切り
パネルの内部仕切りです。高さの違う基板を固定するので、仕切りをで基板の足場を作ってます。
見ていただくとわかると思いますが、3Dプリント品はいくつかの部品に分解してプリントしてあります。理由は下記の理由です。今回は、主には②の理由によるものです。
① 精度の必要な面を下にしたいから
積層していくとどうしても壁面は、密着していないので、わずかですがノズル形状に影響されます。
ですが、ビルドプレート面は、水平なので、きれいな平面ができます。
今回は塗装しましたが、塗装しない場合には、この面を化粧面にしたり、接着に使用します。
② サポート材をなるべく使いたくないから
サポート材を使用すると、どうしてもサポート材接着面があれてしまいます。
サポート材をなるべく使わない様に回転させて印刷すれば、プリント物がきれいに仕上がります。
③ なるべく強度の出る積層方向でプリントしたいから
Z方向はどうしてもフィラメントがのっかっているだけですので、積層面が弱いです。
力のかかるような部品は、積層面を意識してなるべく強度がでるようにプリントします。
次に実際に組み立てていきます。
まずは、3Dプリント部品を本来の形状に組み立てていきます。
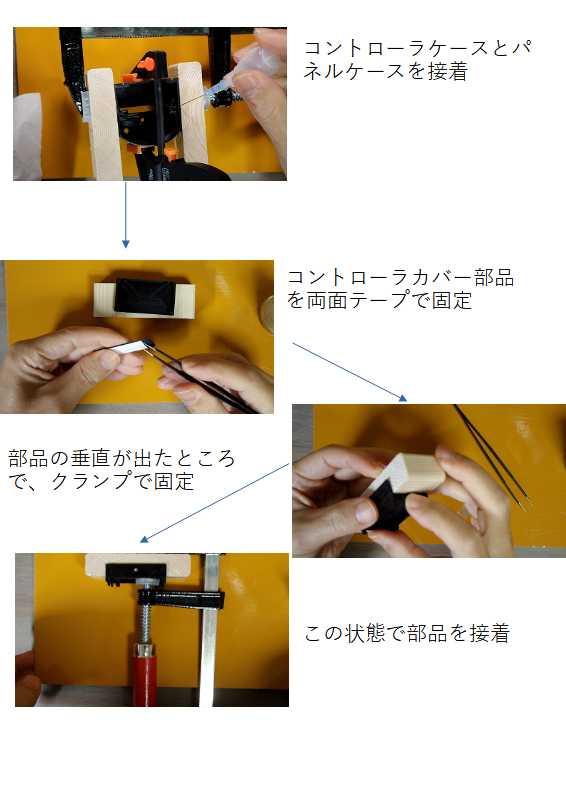
次にパネル部品をくみ上げていきます。
3Dプリント部品にパネル基板、ローターリーエンコーダーを取り付けます。
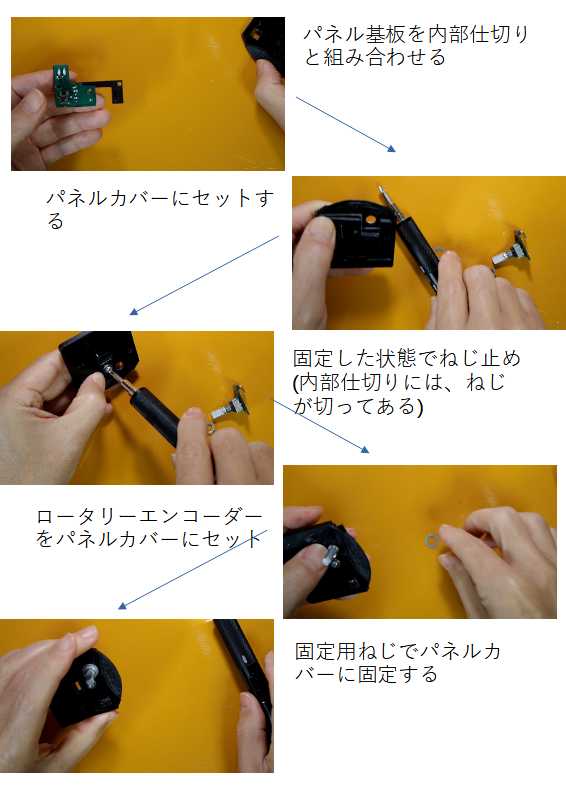
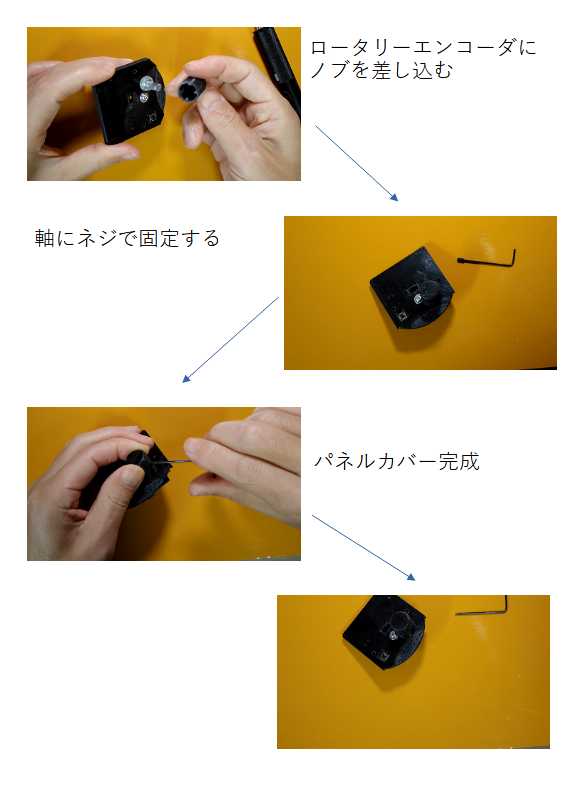
大まかに部品:「ESP32基板」「パネルカバー」「コントローラケース」「ケースカバー」ができ上ったので、まずは、「ESP32基板」を「コントローラケース」に組付けます。
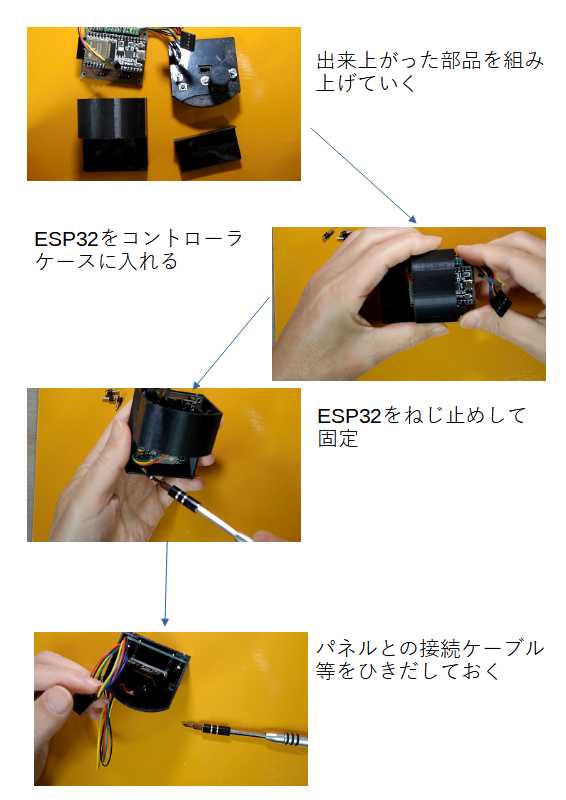
最後に「コントローラケース」「パネルカバー」「コントローラケースカバー」を組付けます
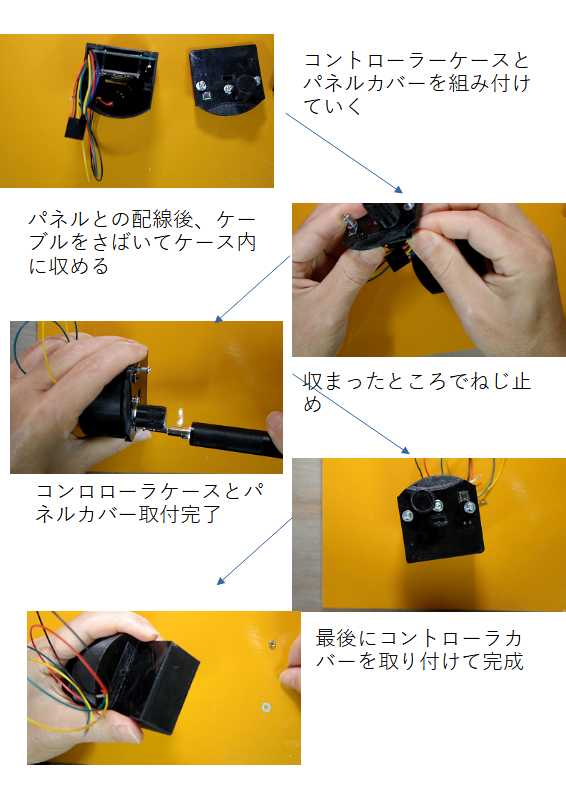
■ 光学ユニット組み立て
まずは部品リストを示します。
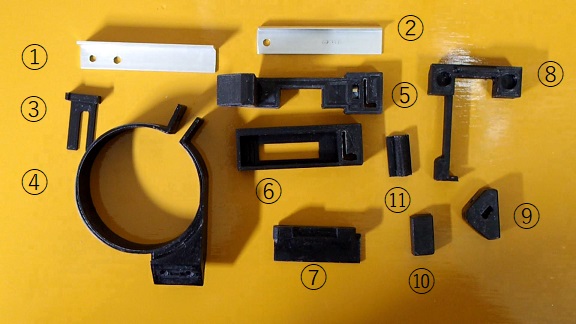
① ミラーユニット表示位置調整用アルミチャンネル
② OLED焦点調整用アルミチャンネル
③ ミラーユニットストッパ
④ 光学ユニット固定用バンド
⑤ ミラーユニット表示位置調整
⑥ OLEDケース
⑦ OLEDケース蓋
⑧ ミラーユニット
⑨ ①のストッパーエンド
⑩ ②のストッパーエンド
⑪ 90度反射ミラー(⑧ミラーユニットのミラー)
光学ユニットの組み立てについては、動画でまとめました。
今まで光学ユニットの仕組みを中心に説明をしてきましたので、ここでは動画で説明の代わりとさせていただきたいと思います。
■ ありがとうございました
長い期間おつきあいありがとうございました。「実体顕微鏡 テスタージグ」は、今回で終わります。
説明が冗長となったり、尻切れトンボになってしまったりしてて、うまく説明できていないですが、またよかったら、お付き合いいただけると嬉しいです。
では、また次回。