今回は、先週に引き続き照明の作成です。
説明は、下記のように行います。3Dプリント部品は、平日夜にプリント済みで作業を開始してます。
おもに作業風景になってしまいますので、ポイントだけかいつまんで説明させていただきます。意外に量がおおかったので、今回は、a~cまでの様子を紹介させていただこうと思います。
a. (まずは)DIYの結果
b. PCBの切り出し
DIY品の基板制作用CNCでPCBを切り出します。
c. レジデントマスク
レジデントマスクをかけておきます。
d. 照明ユニット組み立て
照明ケースと基板を組み合わせユニットを完成させます。
e. USBケーブル改造
最後に照明ユニットとUSBケーブルを改造して電源ケーブルを作成します。
■ (まずは)DIYの結果
まずは、結果から。
3眼カメラで撮影した結果ですが明るさが改善した結果、画像の荒れが目立たなくなっているように思えます。顕微鏡をのぞいていても、今までよりもクリアになったように思えます。結果は良好だと思います。
照明は手元側に装着しましたので、まったく、顕微鏡作業に支障を与えていません。
下図は、効果検証のため、下記を評価したものです。
〇 手元が暗い場合(部屋の照明だけ)で、照明を点灯したときの効果
〇 スタンドを点灯している場合(対象物を照らした場合)で、照明を点灯したときの効果
〇 照明ユニットの装着状況

■ PCBの切り出し
AUTODESK EAGLEで生成した基板生成データをSDカードに入れ、CNCにセットして基板を生成していきます。私は、PCとは接続せず、オフラインで作業してます。
工程は、下記のようになります。①~③は、CNC作業で一連の流れで行います。
① プローブ
今回はビデオを撮り忘れました。
補正に必要な、基板サイズ測定、レベリング計測、スキュー計測を行います。
画像に基板を止めている4つのクランプは、計測用ジグ兼クランプとなっています。
この工程のおかげで、両面基板の制作も可能です。
② エッチングパターン作成
まずは、エッチングパターンを作成します。
0.1mmのVカッターでエッチングパターンを切りだします。
下図は1枚の基板に見えるかもしれませんが、実は、2枚の端材を組み合わせて使ってます。
今回は指先もないくらいの基板サイズなので、ケチって端材を使いました。💦
2枚の端材をあわせて、基板制作用クランプに収めています。
③ ドリリング/ミリング
エッチングパターン作成が終わると、ツールチェンジを行い、その後にドリリングします。
私が使用しているCNCは、自作品ですが、手動ツールチェンジ機能は搭載してあります。
基板制作では使用するツールの種類が多いので、手動であってもかなり便利です。
先端ツール交換タイミングで、規定位置に移動しツール交換を促します。
先端ツールを交換後、再度先端ツール長を計測して取付誤差を取り除きます。
ケーブルがダマになってました(笑)が、ちゃんとプローブは機能してます。
私が基板作成で使用する先端ツールは、ざっと、こんな感じです。
ドリルは主には、DIP部品、基板取付穴用ですが、3種類で足りてます。(EAGLEがあるドリルを適切に選択してくれます。)
エンドミル、Vカッターは銅箔の厚さや基板素材や大きさによって変えてます
0.1mm Vカッター 30°/15°(2種類)
0.5mm ドリル
0.75mm ドリル
0.9mmドリル
1.0mm エンドミル
1.5mm エンドミル 2種類
2.0mm エンドミル 2種類
2.5mm エンドミル
3.0mm エンドミル
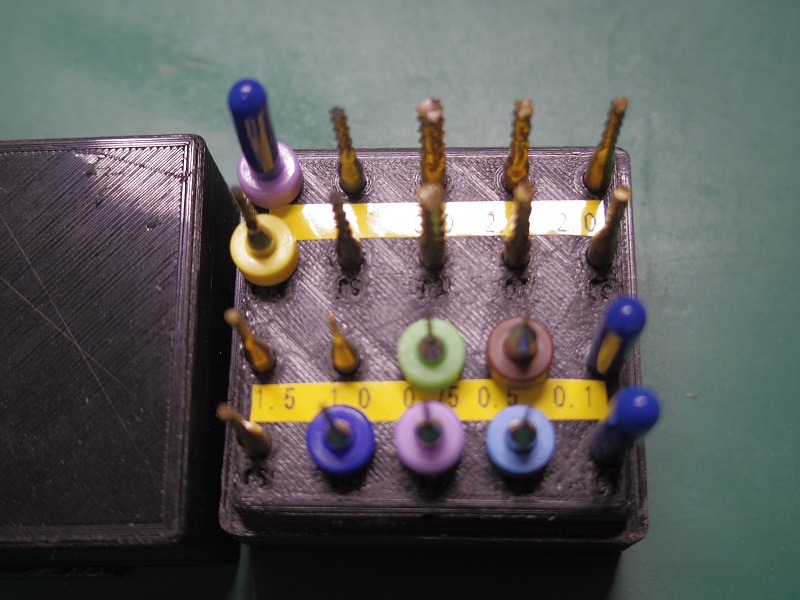
④ 基板チェック
カットした基板の掃除と電気的なチェックを行います。
エッチング時は、10,000回転でビットを回しますので、たまに銅箔が溶けて回りに飛び散りカットしたパターンの間におちていることがありますので、切りカスを取り除きます。
また、基板をカットする際に(エンドミルの切れがよくなくて)、基板周辺がかけてしまうことがあるので、パターンに影響のないとだけ確認しておきます。
大体、0.1mmのエンドミルで切っても、直線:0.25mm程度、曲線:0.5mm程度になっちゃいます。0.1mmでは切れないですねぇ…
0.035mmの銅箔厚に対し、0.02mmほど掘っている(熱で先端ツールが膨張することを考慮して)のですが、私の機材とVカッターでは、この辺りが限界っぽいです。でも、まあ、DIYでは十分です。
DIYでこれ以上の精度が必要な場合は、別のやり方を考えた方がいいような気がします。
この誤差を前提にEAGLEに、エッチングパラメータ設定してありますので、隣接するパターンを壊すなどの問題は(ほぼ)発生しません。
参考程度ですが、私の使用している生基板の銅箔厚は、片面基板:0.035mm、両面基板:0.018mmです。CNCで使用するには、薄いほうが有利なのですが、片面基板:0.018mmは、手に入らなくなってしまいました。
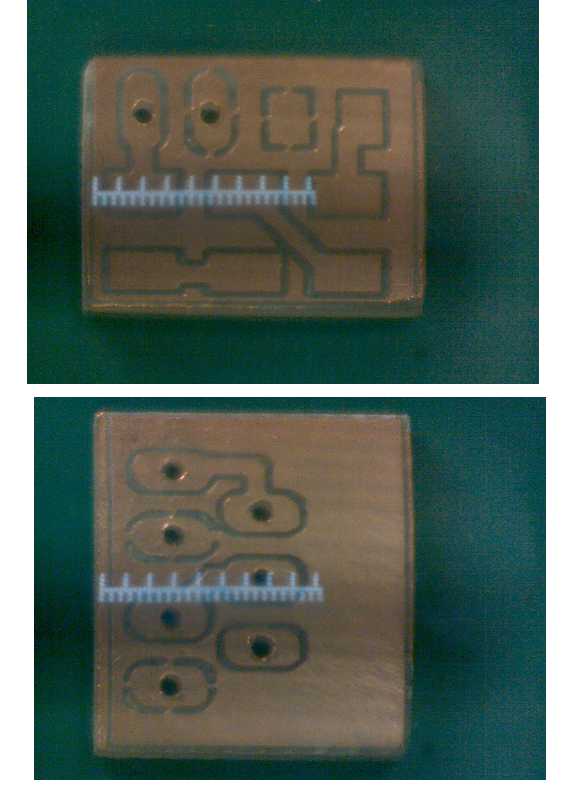
■ レジデントマスク
今回は、基板が小さくてレジデントマスクを塗るのが少々難しく、きれいにはいきませんでした。
これだけ小さい基板は、今回が初めてで、変則技を使いました。
動画にて、指先と比べてみていただければ、大きさが想像できると思います。
両面テープで基板を固定してあるのですが、粘着が利かず、動いてしまいました。
ただ、不細工でも表面実装品を扱うので、施して絶縁した方が面倒がありません。
この工程は、手動作業かつ感覚に頼った作業がおおく、ミスが発生しやすい工程です。
安定的にレジデントマスクをかけるには、専用ジグが欲しくなりますねぇ。
ちなみにですが、軽微なパターンずれ程度であれば、顕微鏡を見ながら手修正します。
(実体顕微鏡がないころは、ルーペと携帯顕微鏡でやっていたので、かなりの地獄でした。)
まったく話にならないほどずれた場合には、アセトンで落としてやり直します。
レジデントマスクの塗装手順は、下記のとおりです。
① OHPシートにはんだ付けする部分を印刷しておきます。OHPシートは紫外線が透過しないよう2枚重ねて使用します。
② 基板とOHPシートの間に、PP(プリプロピレン)を挟みます。PPは100均のクリアポケットを切って使ってます。
③ 基板をアルコールなどで、脱脂します。
④ インクをぬります。今回は基板が小さいので、筆で塗ってみました。
⑤ PP、OHPシートをかぶせて紫外線をあてます。
⑥ ランド部分は硬化されていないので、アルコールを含ませた綿棒でふきとります。
⑦ きれいにふき取ったら、再度紫外線をあて硬化します。
レジデントマスクした後は、銅箔が出ているランド部分をはんだ付きがよいように加工します。
本来だと錫メッキするのですが、今回は、試してみたいことがあり、違う方法を試しました。
メッキは、廃液処理が面倒で、DIYではやってられないので、代替手段を模索中です。
今回は、錫メッキの代わりに、はんだペーストで被膜を作ってみました。
動画では、はんだモリモリにしてしまったので、あとで、吸い取って被膜になるよう調整しました。
結果としては、はんだののりもよく、ストレスはありませんでした。
もう少し手順を改善すれば、盛りすぎなどの失敗はないと思いますし、メッキ処理の代わりに使えそうです。
■ 続きは、次週
次回は、組み立ての様子を中心に紹介させていただきます。
また、よければ見てやってください。