私は、1品モノの基板を制作する場合には、自作のCNCを使って、両面基板、片面基板を制作しています。製造枚数が多い場合や、高精度の基板が欲しい場合は、海外発注しますが、大概のモノは一品モノなのでCNCで自作する機会が多いです。
概ね思い通りに制作できていますが、レジデントマスクを制作する工程だけは、納得がいかない点があります。現在は、OHPシートに露光用パターンを印刷してインクを紫外線で焼き付けていますが、この方式には、以下のような問題があります。
- マスクしたい箇所が露光してしまう
OHPシートの印刷図形は、マスクしたい部分がベタ塗りされていても、紫外線が透過してしまいます。これは、ベタに見えてもディザが入っていたり、インク自体が透過性であったりするので、どうしても紫外線が漏れてしまいます。
この影響で、たまに、ランド面が汚れてしまい、はんだののりがわるくなることがあります。
マスク部、非マスク部の境界面がはっきりせず、少し、ぼやけた感じになります。 - OHPシートの値段が高くなってきている
OHPシートの需要が減ったせいで、だんだんと値段が高くなってきたのと、選択範囲が狭くなってきました。紙媒体やOHPでプレゼンすることも減るので、おそらくは、今以上に入手性は悪くなるかと思います。 - 工程が面倒
位置決め時に基板、OHP(数枚)、PPシート、ガラスなどを重ねて露光するので、作業が煩雑です。基板とOHPの位置合わせは気を使いますので、開始するまでに基板、OHPシート、PPシートをテープで固定する作業が必要となります。気を遣う上、面倒で、時間もかかります。
今回私が作成したいと思っているのは、OHPシートの代わりに液晶でマスクパターンを作成し、紫外線露光する装置です。簡単に言えば、DLP(光造形式)3D プリンタの露光部分となります。
とはいっても、3Dプリンタを使用しても制約が発生し、納得のいくものにはならなそうなので、自作していこうと思います。
この制作に関しては、アイデアを絞り出したり、試行する時間が必要なので、更新が不定期になるかもしません。進捗があったら更新していこうと思いますので、たまにのぞいてやってください。
■ 紫外線露光部
下記は、今考えている紫外線露光部です。これが思考のベースとなるかと思います。
今考えているプロセス、それを実現するための課題は、後ほど共有しようと思います。
この露光機ですが、排熱処理とミラー部に関しては、Stefan Burgerさん作の「FDM printed SLA-Printer by TOS」を参考にさせていただきました。
排熱処理は、素晴らしいアイデアでヒートシンクを3Dプリント品で固定されており、真似させていただきました。
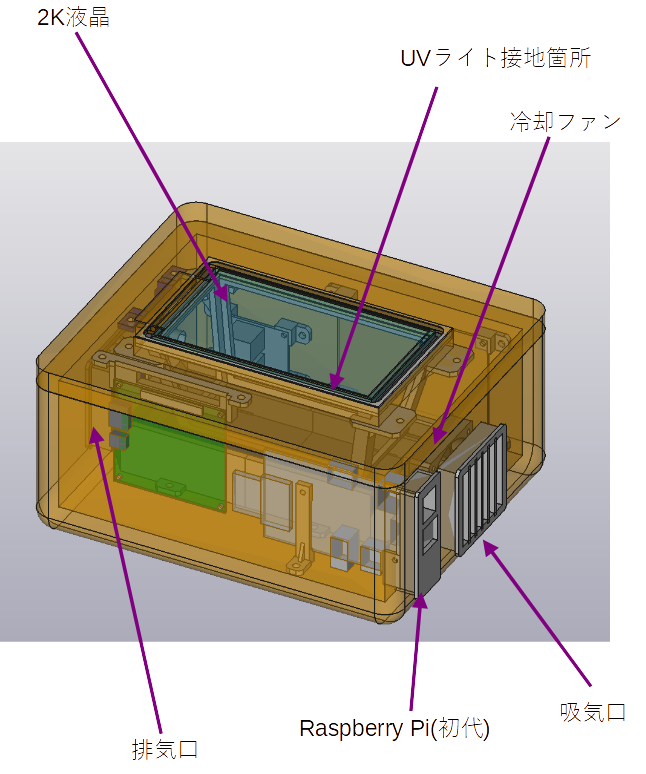
図を補足します。
- 2K液晶
液晶は、Sharp LS055R1SX04(2K液晶)を使用します。
理由は、購入当時は、お手頃値段だったことと、かなり面倒くさそうですが、Raspberry PIでハンドリングできそうだったからです。今では、結構なお値段がしますので、お手軽ではなくなりました。 - UVライト
2K液晶の真下に配置し、液晶を下から照射します。 - Raspberry PI (メインコントローラ)
今回は、2K液晶(MIPI)を使用するので、Raspberry PIを使用することにしました。
制御の都合から、HDMIがあつかえることと、GPIO等の制御を行う必要があるので、手元にあるものを使用します。(知人が捨てようとしていたものをいただいただけです。)
ダメな場合は、もう少し新しいバージョンのRaspberry PIに変更しようと思いますが、まずは、初代Rasberry PIでスタートします。 - 電源類
UVライト、Raspberry PI等を制御するための電源ですが、12V DCを考えています。 - ミラー
図では設置位置を記載していませんが、UVライトと2K液晶間をミラーで囲う予定です。
2K液晶の端から端までなるべく均一になるように照射します。
レジデントマスク程度なら、露光時間はおそらく10秒もないのですが、後々、色々と使えるようにしておきたいので、UVライトの下には、ヒートシンクと冷却ファンを搭載して、安全性をたかめておくことにしました。
■ 想定しているプロセス
ここでは、レジデントマスクを露光するまでのプロセスを記載します。(今考えていること)
〇 露光前提条件
前提条件として、エッチング済み、ミリング済みの基板に対して、レジデントマスクを露光することを考えています。露光は表、裏の片面づつおこないます。
〇 露光までのプロセス
- 露光面にレジデントマスクのインクを塗布します
- インク面を下して、エッチング済みの基板のランド、ホール位置と液晶に表示されるマスクの位置調整を行います
- 紫外線を照射して露光します
ここまでですと、簡単なように聞こえるかもしれませんが、エッチング済みの基板を取り扱うので、色々と考えないといけない点があります。ランド、穴とマスク表示位置をあわせるのは、結構面倒くさい上に難しいです。大概これで失敗することが多いです。
■ 基板、露光装置の位置合わせ方式
いくつか方法はあると思いますが、どの方法も色々と問題があり、現時点では方式を決め切れていません。実は、メカ的には、ここが一番の課題です。
- 液晶表示位置を調整する方法
基板のランド位置、ホール位置を目安に液晶表示位置を調整します。
ですが、この方法をとる場合、位置調整後にインクを塗布するなどのプロセスを取る必要がありそうです。目視方法も、簡単に液晶の下からの覗くわけにはいかないので、検討が必要です。 - 機械的に位置調整する方法
これができれば一番簡単なのですが、これもなかなかに難しそうです。
基板をミリングした場合、エンドミルのブレや基板との接地角度の関係で多少誤差が発生します。
大体実測すると、基板をミリングした際の誤差は、0.1mm~0.3mm程度あります。
基板面積が広い場合、この誤差はかなり効いてきます。
■ 次回
次回は、基板と露光装置の位置合わせを方式を考えようと思います。
現時点では少々苦しい感じしますが、次に進むことのできるアイデアを練ってみようと思っています。
またよかったら、のぞいていただけるとありがたいです。